Table of Contents Show
Smart contractors are always on the lookout for ways to save time and money. Everybody knows that. Fortunately, thanks to advances in design, engineering, and technology, systems have been designed that allow contractors to perform work with greater speed and accuracy, which saves both time and money. Tunnel formwork is one of those advances.
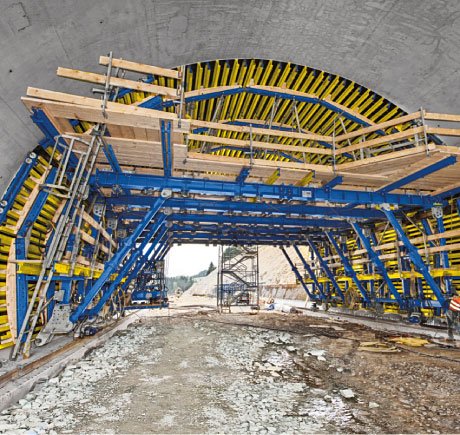
A Tunnel Formwork System allows a contractor to cast slabs and walls in a single operation on a daily cycle. It combines all the advantages mentioned above with the accuracy of factory/off-site production while still retaining the economy and flexibility of in-situ construction methods.
Just a few of the benefits of this method are listed below.
Quality
Tunnel formwork allows the quality of a project to be maintained despite an increase in construction speed. The steel facing of the formwork creates a smooth, high-quality finish that can have direct decoration with a minimum of preparation work, reducing costs and time savings.
Design
Tunnel formwork allows large bays with exceptional flexibility in terms of design. This also affects the layout of the project and allows a higher degree of flexibility for the finished project. As design applications expand, so do the number of projects this formwork will apply to.
Building
Tunnel formwork can be adapted to fit every project. The nature of tunnel formwork allows reinforced mats/cages and prefabricated forms which makes the entire construction process much easier and produces a fast and smooth operation. The techniques are already common in the industry, which causes less reliance on skilled labor.
Safety
Tunnel formwork has edge protection systems and integral working platforms. Further, the repetitive nature of tunnel formwork encourages familiarity with the operation and after training is finished, the productivity of workers is increased as a project progresses toward completion.
The need for specialized tools and equipment is minimized as moving the tunnel form minimizes the occurrence of accidents on sites.
Sustainability
There is practically no practice that tunnel formwork doesn’t affect in a positive way, whether it’s the in situ casting of units on a site, the availability of concrete supplies, and transportation requirements. The materials and methods are the same. It is just the methodology that changes, which only does so for the positive.
Tunnel formwork affects the delivery of materials so that just-in-time processes are optimal. Further, there is zero waste in terms of both materials kept on hand as well as when construction progresses. This results in a tidier site, cost savings, and benefits in safety.
The nature of concrete allows it to be formed better with tunnel formwork processes. This provides better insulation and boiler design issues. Heating and air conditioning costs are minimized too.
By now, tunnel formwork is no secret. Even its benefits are well known. Further, as tunnel formwork is incorporated into a growing number of projects, it will be found that its capabilities will be expanded and increased.
There can be little doubt that, as these applications increase, so will the expansion of projects that tunnel formwork is used on, which will result in further uses. It’s a chicken or the egg situation, with applications leading with the benefits listed above, and in turn leading to more applications. The good news in all of this is that everyone—builders and clients—enjoys the benefits.