Table of Contents Show
Plastic molding is a simple process capable of making complex parts and items. It’s a process of pouring liquid plastic into a mold or cavity so that it takes the geometry of the mold using a plastic molding machine. These plastic molds can be used to produce a wide range of products.
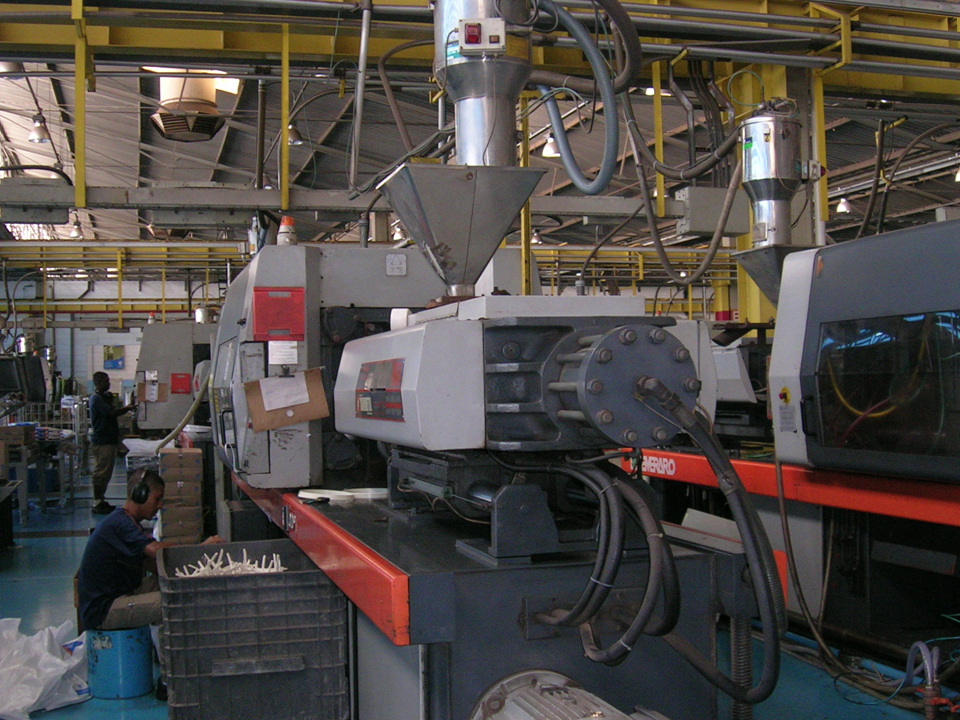
There are five most popular and preferred types of plastic molding. These types of plastic molding include extrusion molding, compression molding, blow molding, injection molding, and rotational molding.
Each of these types of plastic molding will be elaborated on in subsequent paragraphs below.
1. Extrusion Molding
With extrusion molding, melted plastic is poured into a hole to produce a shaped plastic part. This designed shape that the melted plastic gets poured into is called a die.
This die is specially designed for a specific outcome. The process is similar to putting the dough in a press to make shaped cookies.
The other types of plastic molding also use an extension to pour the molten plastic into the molds, the only difference being that other forms use the molds to make a specific shape; meanwhile, the extrusion itself uses the die’s shape to make the shape.
2. Compression Molding
The process of compression molding involves pouring the raw liquid into a heated mold where it’s being compressed together to create a specific shape.
The material is put through extremely high pressure to ensure the finished product comes out fine and strong. The process is rounded off by cooling the liquid plastic so that it stays in shape before its removed from the mold.
3. Blow Molding
The blow molding process makes the plastic parts come out hollow and thin-walled. This method is the best option when the plastic part needs to have the same wall thickness. The process is similar to glass blowing.
The machine melts the raw plastic to a liquid point and then pumps air into it like a balloon. The air helps the plastic to take the shape of the mold as it gets blown into it.
After the liquid balloon fills up the mold and takes the geometry of the mold, it is cooled to maintain its shape. The process is a fast one, and with it, you can produce up to 1400 parts within a 12-hour duration.
4. Injection Molding
Injection molding follows the same process as extrusion molding. The only difference is that with injection molding, the molten plastic is poured directly into a specially designed mold.
The molten plastic feels up the mold under high pressure and takes the shape of the mold. The plastic is left to cool to maintain its new shape before the mold is opened and the finished product ejected.
5. Rotational Molding
Rotational molding, or roto-molding, involves pouring the resin or liquid into the mold and then rotating it at high speed. The liquid then spreads evenly across all the parts and crevices of the mold.
Then the mold is cooled so that the plastic can maintain its new shape before it’s removed from the mold.
This process helps to save production materials, and it’s more economically and environmentally friendly.